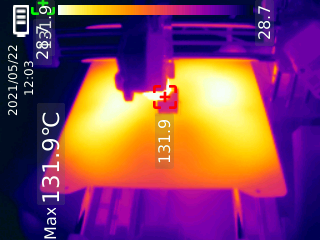
I’ve ordered this 3D printer in the beginning of 2021, after initial successes with having a few models printed out by my friend. Once I put it together, it was amazing to just watch it materialize models from various sources.
Solvespace has turned out to be a very good program for modelling custom objects, after I had to resolve some of its issues, notably accidental slowness. In general, my relationship with this software can be described as love/hate—it is easy to understand, but limited in features, and has erratic export issues when you inevitably manage to break its NURBS mode and have revert to triangle meshes.
I bought a 3Dconnexion SpaceMouse in an attempt to make it easier for me to work in the CAD, but I’ve eventually learnt how to use the mouse with similar ease—you need to press Ctrl/Shift intermittently as appropriate.
Průša Slicer is a fairly good program as well, though it would be nice if it could also command the printer to print over LAN.
hooks to hold cables on my computer desk
a holder for my Geiger counter
a stand to scan books with my phone
an adapter to keep another strainer centred in my kitchen sink
a holder for charging 18650 batteries with the RD6006P laboratory power supply
Future projects:
hard and soft EUC attachments
a replacement container for drawers from another, discarded container—I’ve got a rough concept that consists of three kinds of intertwined parts and can be lifted by the top
rotating rings toy can’t be injection molded, nor disassembled
assault whistle is indeed painfully loud
AR-15 speedloader works nicely with my CZ BREN 2
Aztec death whistle isn’t exactly perfect but it certainly is loud and fun
Tricks:
raising the heatbed temperature can make lifted corners lie back down
heated knives easily cut through anything that is stuck
thin strings are quickly removed with a lighter
Materials:
PLA is really hard and prints very accurately
PETG is somewhat softer and can be easily shaved with a knife, but it also strings a lot
ASA is also softer, has a very weak but lung-aggressive smell, requires a ventilated enclosure, and sticks to the textured PEI sheet a bit too well (it seems to help to set the first layer a bit higher, though that makes for uglier surfaces)
you can’t really have transparent prints with FDM printers; transparent PETG also likes to stick to the nozzle, get dark brown with heat, and randomly stain the print
Modelling principles:
screws can go directly into the plastic, especially with softer materials, and this approach is also used on the printer itself
Filament storage bags don’t hold vacuum indefinitely but are otherwise almost perfect.
Copper brushes so that brass nozzles don’t get scratched.
Silicone socks specifically for this heater block, although V6 socks generally work as well.
Roughly around the time when I changed the nozzle to the wider 0.6mm, which is much faster at printing and I’d like to use it as the default, I started getting extruder clicks during retraction, and holes appeared at seams when printing PETG as well as PLA. This has remained the case even after returning back to the standard 0.4mm nozzle.
I tried doing these things to make the problem go away:
cleaning out the extruder itself, which did have strands of filament in it
cold pull, which appeared to be a no-op, and the pulled-out piece of filament looked almost exactly like the example photo
replacing the inner PTFE tube in the hotend with the spare one
toying around a bit with the idler tensioner screw
regreasing the rails, which did at least make it run quieter
changing the long PTFE tube
realigning extruder gears could rather make it worse, and I got a blister as a bonus
changing the nozzle temperature to 230..270 C (PETG)
I’m also not sure why the idler moved so much during retractions:
Desperate, I ordered the Bondtech extruder and heatbreak, as well as some thermal paste. Someone claimed they’re required upgrades for printing from flexible materials, anyway.
Installation of the extruder wasn’t particularly involved, and the official guide was fairly straight-forward—I just used a little screwdriver rather than a hobby knife for the pre-4.3.3 connector adjustment (do they like cutting themselves?) The hardest step was extracting the input PTFE tube that Průša staff inserted fairly violently into their extruder, and has some scuff marks to show for it.
After that, I was immediately met with the first issue of the alternative extruder: it can’t even load the filament right without the proper E-step setting, as it won’t reach the nozzle. Otherwise… it hasn’t quite reached my hopes and expectations, but I’m happy with it. The printer is much quieter now, even doing something as simple as loading the filament, which used to be very loud. However, the clicking isn’t gone yet, it just isn’t nearly as annoying. Retractions still appear to cause issues in prints, and in this aspect I’ve managed to get exactly where I was before.
There is one ugly aspect to this extruder as well: the tensioning screw is quite difficult to set up right, and you have to experiment.
Work on figuring out the best settings. Notably:
printing temperature for different kinds of filaments
obtain or make a linear advance tuning file for the Mini+ (the i3 one I found was dangerous, but it might be able to fix it by inserting missing G-code for bed levelling), even though Průša claims that everything is already perfect by default
Things to test:
one AR-15 speedloader ram print had corners mysteriously curling up, and it happened again later on the death whistle: temperature, fans?
Simplify3D has some general guides
Průša page about hotend troubleshooting plus comments
https://www.youtube.com/watch?v=wxxLOwe2gJs and the comments
All filaments release measurable volatile organic compounds when printing, as well as nanoparticles, and I plainly felt something wrong with my lungs, even with PLA and PETG. Moreover, I wanted to try ASA, which besides reportedly smelling much more requires stable temperatures. I needed an enclosure.
While thinking about how to go about this, I made a trivial enclosure from an IKEA LACK table and some food wrap. While it prevented dust from falling onto the printer, it was otherwise perfectly useless, what with its impractical size and weight. Also, simply stacking them wouldn’t give me enough room to put things underneath.
After some research, and looking through the IKEA e-shop, I arrived at the decision to formalize my impromptu ugly stack of things in the form of a PLATSA-based build. And I got it right only due to sheer luck—while the 40 cm high glass door I picked was insufficiently high to cover the whole printer, the drawer front had an alternative, lower groove for the bottom, which enabled me to cover exactly the blank space above it. Very little space is wasted.
The quality is sadly appropriate for the low price, in that the door had some resolvable issues with closing flush, because the side walls of the assembly warp outwards under load, and the freely hanging shelf is unable to hold them together.
PLATSA frame 60×55×120 cm, 503.309.46
HJÄLPA shelf 60×55 cm, 903.311.66
VÄRD glass door 60×40 cm, 003.845.07
FONNES drawer 60×57×20 cm, 603.309.79, 803.859.23
2× HJÄLPA soft closing hinge, 903.828.82
The bottom part is open intentionally, in order to help dissipate heat from power adapters, and charging devices.
I applied some unused foam tape to seal the huge air gaps around the door at least the tiniest bit better—it even looks nicer that way. Similarly, I had to mask the ugly connecting screw holes—for that I used Prusament ASA "Signal White", which is actually just regular boring white and roughly matches the paint on the frame.
Due to insane resonation levels, I’ve placed the printer on a tile that I cut with a cheap cutter to about 51 cm of length (the shelf is 52.5 cm long), supported by a few rather dense felt pads, as felt is known to have good sound insulation properties. Originally, with stock Průša feet, there were exactly 2 cm of vertical space left above the Z axis stepper motor—the padded tile reduced that to 8 mm, which is rather acceptable. (Note that the Z axis will be slightly limited in movement, as the PTFE tube and cable bundle will start to bend at the height of about 130.) As for the practical results of this exercise, purely subjectively judging, it seems to have helped, reducing the direct transfer of vibrations a great deal. More empirically, when printing with the glass door closed, I measured 52 dBA max just outside of it.
There is also a 50 cm USB 2 extension cable now (theoretical maximum 60 MiB/s, therefore more than sufficient for G-code), since trying to find the hole was fairly anoying even without the enclosure, and the keyring tended to make noise.
To tidy up the cabling, I used a hole saw to make a ø 5 cm hole in the back for my UPS’s power cable, though ø 45 mm would have more than sufficed. Power plugs are less than ø 40 mm. To make the slightly botched opening look nice, even though it stays hidden at all times, I’ve printed a perfect bushing, and glued it in place with PVA glue:
Next, the back panel flexed a bit too much, and there was about 16 mm of space behind it to put a support in. I cut off a piece of a rectangular 20 by 5 mm aluminium profile, and stuck it there using double-sided tape. The profile proved to be quite difficult to cut with hand tools, yet at the same time it hasn’t stopped the flexing—I should have went for something even more rigid.
With this in place, I had to make the printer’s power cable go through the middle of the shelf—I cut a semi-circle-ish shape with a jigsaw, filed it into something better resembling a semi-circle, then printed an appropriate grommet.
After building a new kitchenette light, I had enough leftovers to make an appropriate light for my printer.
I found a PSU that could be used to power the light, but it gave 12.19 V, and I wasn’t sure if that value is okay. People claim successfully using LED strips in cars, where the voltage can be as high as 14.5 volts, but that still doesn’t provide much confidence.
So I ran the numbers. Going by per-module resistor values, different for each of my two strips, the current cannot be more than (12 V / 180 Ω =) 66.666 mA or (12 V / 200 Ω =) 60.000 mA, but this is further reduced by the diodes. In particular, when assuming a voltage drop of 3 volts per diode, a somewhat typical value, the target current is about ([12 - 3 * 3.0] V / 200 Ω =) 15 mA, way below the listed "absolute maximum rating" of various 2835 LEDs one can find on the Internet.
In general, mildly higher voltages affect life span, but they’re nothing to worry too much about—the bigger concern is proper heat dissipation.
Since the light strips are unnecessarily powerful, I ordered a basic dimmer from AliExpress, which has caused me considerable pain—never mind that it contains a very weak MOSFET that will burn on higher loads, but the switching frequency is set way too low, below 100 Hz.
I’ve laboriously found out that the necessary frequency should actually be in the order of tens of kilohertz, because:
100 Hz, equivalent to rectified 50 Hz AC, is about the very threshold of sometimes being able to see lights flicker directly for most people, but it’s a stroboscope.
With digital cameras, if the frequency isn’t exactly 100 or 120 Hz—which is unrealistic with a 555-based circuit—or when you point them directly at the light source, their anti-banding will fail. Multiple phase-shifted light sources also break it. Moreover, SLRs without ‘flicker reduction’ may produce entirely black photos.
At 1 kHz, there is still a noticable stroboscopic effect—when I wave my hand quickly in front of a light, I can see it in multiple copies, and moving my eyeballs has the same effect on everything illuminated, which is really annoying. Wikipedia summarizes this subject rather well.
At 10 kHz, my phone’s camera still shows the duty cycle as distinct vertical stripes, and my DSLR as horizontal. It’s also within the audio range, so you can get piezo noise.
The problems have mostly went away once I bumped the circuit’s frequency to somewhere around 35 kHz. This change was rather simple to achieve, because the board happens to use the familiar NE555 in its astable mode, so I kept progressively replacing a nearby 100 nF SMD capacitor with lower values. The winner was 220 pF.
First, I managed to attach a TK783 THT ceramic capacitor from my Tesla stockpile, but then I bought a proper set of 0805 SMD capacitors—both can be soldered onto 0603 pads just fine with a bit of effort. I had great success with using flux, solder wick, and a knife tip to remove small SMD parts.
I actually kept experimenting with the frequency on separate test circuits, and with LG Nexus 5X I’ve managed to find hints of aliased stripes even at 200 kHz, which is ridiculous. My conclusion is that PWM should be avoided at all, if possible, and I haven’t even touched colour. Otherwise, something between 20 and 50 kHz seems like a good compromise—higher frequencies than that have diminishing returns, and you may start getting other issues.
Of course, while trying to attach oscilloscope probes, I managed to short out the cost-optimized transistor. I’m not sure how much current my 2A power supply put through it, but it blew within seconds. Luckily, semi-blindly replacing it with LR7843 has worked out perfectly, and I no longer need to care about longevity. Notice how the proper part costs 10 fucking cents per piece.
While I ended up using my hot-air station to seat parts properly, it didn’t seem necessary, as you can solder the MOSFET’s tab from the side.
Well over $1000 in equipment to fix a $2 dimmer, and to get a bit of experience.
As already mentioned, the sides warp outwards, which could be resolved by pulling them together in some manner—perhaps using a threaded rod or pipe.
I’d also like to connect the printer to the network again, however useless that is, or maybe just Wi-Fi enable it.
I’d like to add a temperature and humidity sensor with a display (or see how responsive analogue ones are). I could finally make use of my MSP430 dev board, and get sensors from Aliexpress.
Air filter inspiration: 1, 2, 3. People claim something as relatively simple as a HEPA + carbon filter even on low fan speeds gets rid of ABS odours, so there’s probably no need to overengineer. HEPA-rated filters can be most easily obtained for vacuum cleaners (1, 2, 3, 4, 5). Active carbon can simply be bought in pellets. A large and powerful fan is approprate (1, 2, 3). PWM fan control would be possible. I definitely need temperature regulation and ventilation for longer ASA prints, not only to avoid damage to the printer, but also to prevent spools themselves from getting too hot.
Any controls shouldn’t be put it in there with the printer. I can screw into the premade holes in the side, below the drawer. Print a case using my signal white ASA filament.
In short, this is a time sink, though the experience should be valuable.
List of usable parts at my disposal:
partial TI MSP-EXP430G2 LaunchPad development kit with MSP430G2553, ±3.3 V
plentiful 7-segment THT LED displays: LQ425 ×7, LQ310, LQ410 ×2
I2C OLED module 3.3–5 V would be a much simpler and nicer solution, I have two
plentiful switches, tiny and large
I placed a closed glass bottle with muriatic acid next to the printer, which proceeded to promptly rust from the vapours. While the printer kept working as it used to, all bearings, most screws, and to some degree other parts got properly rusted.
Dismantling and rebuilding the printer was a very painful process. I had to order a lot of new parts, including a new Z-axis step motor, which I probably broke myself, and new hotend parts, because it could no longer be disassembled. I also couldn’t manage to re-sleeve all the hotend cables the way they’re supposed to, so I had to give up on trying to cover the electronics—perhaps you’re supposed to sleeve cables from the bottom up.
I used this opportunity to install the stainless steel Bondtech heatbreak, which was one of the few remaining things I hadn’t replaced in my trials to fix print quality issues.
Alas, what I got instead was random overextrusion.
Resources:
For this occasion, I got a fancy torque wrench capable of being set to 1.5 Nm, of which there are surprisingly few. The first attempt at installation I had completely fucked up, with molten PLA getting into my threads.
Try to print some flex: I could make use of some attachments to my Ninebot One S2 EUC, and it would be handy to print some gaskets.
Try drying out my filaments: put them in the oven at a temperature they don’t warp at, whatever kind they are. Over a long enough period, the moisture should be gone.
Comments
Use e-mail, webchat, or the form below. I'll also pick up on new HN, Lobsters, and Reddit posts.